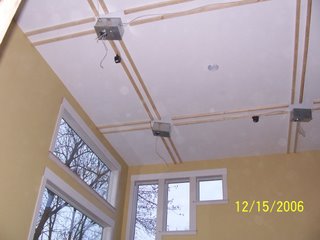
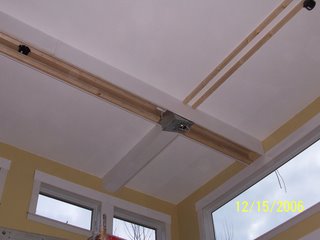
It was a busy weekend. The wood nailers were already installed, but on Friday I finished up the wiring and, at the end of the day, we had most of one big beams (made with 1x10s) up and all of one small one (made with 1x8s).
I told the builder that I'd pre-build all of the small beams so they could be cut to size and that I'd prep as much of the large beam parts as I could over the weekend. Then we could all work together on Monday to put up the parts.
Saturday morning, I set up a long table with a 16' 2x10 and a couple of 16' 2x4's on edge. I organized all the parts and tools and got started. The small beams all have a "routered" dado to accept the bottom panel. To my surprise, I had the parts all done (cut, routered, glued and nailed) before noon so I just started putting them up. With some help from the wife on the long parts, it was all done by 5pm on Sunday. (this also includes a "break" Satruday night were we grouted the kitchen tiles).
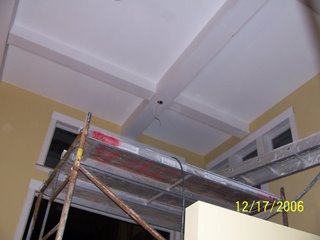
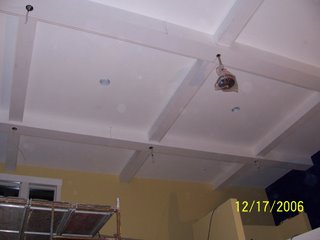
There is a lot of nail-hole filling and seam caulking to do, but I think these just look awesome! The pictures don't do justice to how it changes the feel in the room.
Plus, it gives me a place to mount lights (including track lights on the side of some outer-most beams) that don't create spots for warm air to leak out. Sure, there are a couple of IC cans and a couple of HVAC supplies in the ceiling, but much less than I would have had if I had to put all the lighting through the ceiling sheetrock.
(PS - white painted MDF trim may be scoffed at by some, but, for my skill level, it is wonderfully forgiving with a little caulk and putty. . . Also, in case anyone is wondering, the beam support nailers are screwed into the trusses and to some preinstalled supports between trusses with 4" screws)